The bottom paste process of traditional paper yarn composite bags mainly adopts the method of artificial bottom paste, which has low production efficiency, uneven specifications and low quality; practice shows that in the case of producing paper bags of the same specification, the bottom paste can be improved compared with manual sewing. 20% capacity, 8% paper saving, 12% cost reduction. In order to solve these problems, the packaging industry urgently needs an automatic bottom paste equipment to reduce labor costs and waste materials and improve efficiency.
Traditional artificial bottom paste is divided into two ways: artificial seam bottom and artificial bottom paste.
The specific steps of artificial bottom sewing are as follows:
(1) Prepare the produced paper tube, use the sewing machine, yarn and glue for sewing the bottom;
(2) The worker dips the yarn in glue and installs it on the sewing machine;
(3) Use a sewing machine to sew one end of the paper tube through glued yarn;
(4) Paste the valve port on the other end of the paper tube and sew it with glued yarn;
(5) Spread out the paper bags sewn at both ends to dry, and complete the seam bottom work of the paper bags.
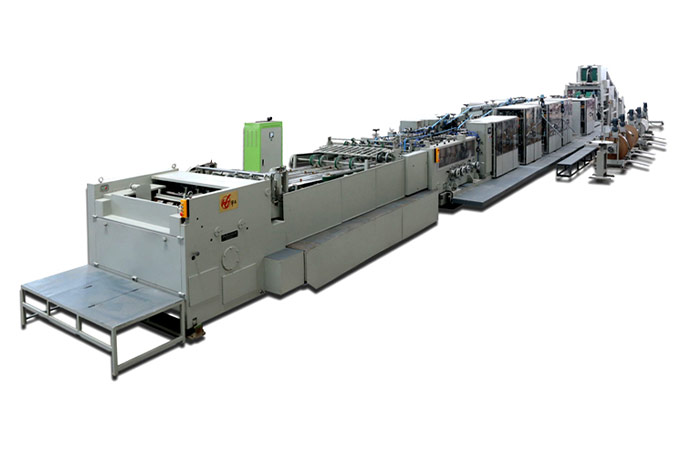
Traditional artificial bottom paste process:
(1) Workers mark the position of one long indentation, two 45° indentations and two vertical indentations on the paper tube, and manually indent and cut them;
(2) Unfold the bottom of the bag and fold two indentations manually;
(3) Manually apply glue on the designated area at the bottom of the bag;
(4) Paste the valve port on the bottom end of the bag;
(5) Manually close the bottom of the bag along the crease, put it into the machine for compaction, and complete the bottom paste work.
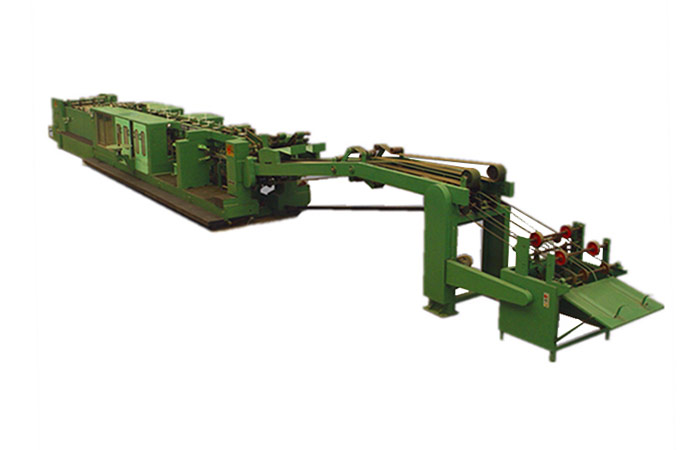
The analysis of the process of artificial bottom paste shows that the paper yarn composite bag square bottom machine first performs the indentation and incision process on the unprocessed bag tube, and indents the surface of the bag along the horizontal and 45° directions, and vertically according to the width of the bottom of the bag. Incision, and the horizontal indentation of the bag tube is relatively easy to achieve, so the bag tube is conveyed horizontally at this time; secondly, the bottom of the bag after the indentation and incision is unfolded along the crease by using a suction cup, and the bottom of the bag is conveyed vertically at this time After flattening and compacting the bottom of the bag after being sucked open, two horizontal indentations are made on the bottom of the bag after expansion; Glue coating and valve sticking; finally, after the bag tube passes through the hemming device and the compacting device, the hemming and compaction are formed to complete the bottom paste work.
By analyzing the characteristics and functions of the process flow of the paper yarn composite bag square bottom machine, the basic requirements of each process of the square bottom machine are obtained: firstly, the bag tube is sent to the indentation and incision process, because the indentation and incision affect the success of the subsequent paper bag. Unfolding, so the accuracy of the indentation and incision is high, and the trace incision is only long but not short; the second beat process is to control the paper bag to enter the suction opening process accurately. When the paper bag enters the suction opening process, it needs to reach the best suction opening position, and the time control is very strict.
The suction opening process needs to suck the paper bag open, and its vacuum system must be strictly designed; the glue application process requires accurate glue application position and moderate glue amount, otherwise the paper bag will have problems such as overflowing glue and not sticking firmly; the valve sticking process needs to be done during the movement of the paper bag The center sticker valve is fast and accurate in position, and the valve port does not fall off after being pasted; finally, the paper bag enters the folding and compacting process, where the paper bag is folded along the crease and compacted into shape, at this time, the bottom of the folded bag needs to be kept from falling apart , The shape is beautiful, and the paper bag does not wrinkle or overflow glue during the compaction process.